THE COST OF CRANE RAIL QUALITY: HOW NOT TO LOSE USD 35,000 A DAY
Choosing the right container crane runways is of utmost importance as Maarten Impens, CEO of Gantrex explains…
Unless you are Bill Gates or Warren Buffett, USD 35,000 is a lot of money no matter where you are from. Imagine being given this amount of money on a daily basis. What would you buy? I know what would be top of my list. Now imagine losing this money on a daily basis, a much less pleasing thought. Well, this is roughly what happens when a busy container terminal has to stop operations of a single Ship-to-Shore crane. Assuming USD 75 per container move, 30 moves per hour, 24 hours operation and an utilisation rate of 65%, multiply 75 by 30 by 24 by 65% and the outcome is USD 35,000 a day, for every crane that’s not in operation.
For a typical berth length of 300 meters with 3 STS cranes, this means a potential cost of around USD 100,000 every day. Granted, not every terminal around the world reaches the above numbers, but the truth may not be far off even for smaller, less busy terminals. And even if the cost is only half, it is still a lot of money for any manager or company.
THE COSTS OF A NEW GREEN FIELD CONTAINER TERMINAL
Green field container terminals can be built in a variety of ways. The investment cost differs immensely depending on the requirement of dredging works, land reclamation, soil quality, and design of foundation and super structures. Then there are the variations in civil contracting, depending on labour costs around the world. And finally, the investment costs for STS cranes which varies depending on the supplier, the design, the components and the origin. To estimate the cost for a new green field terminal is a task that even top specialists in the industry find challenging. Gantrex has done the research by interviewing industry specialists and found the results to vary significantly depending on the above factors. The figures in the following example are an average of our research and should be considered as an indication only.
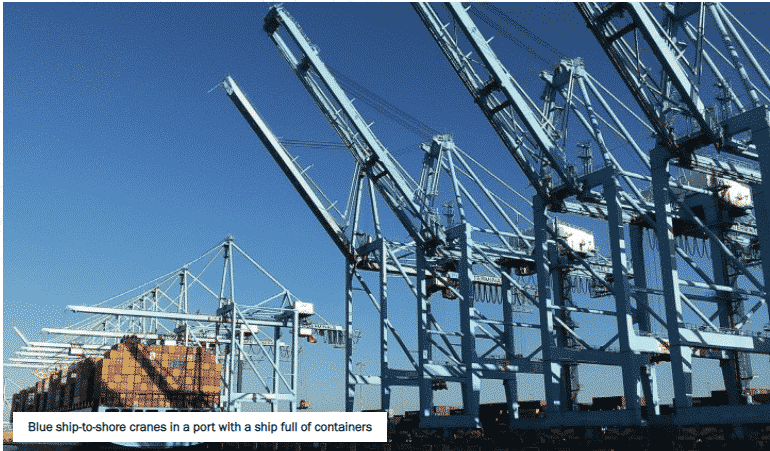
LET’S HYPOTHESISE
Let us build a fictitious new gateway terminal. In reality, a new terminal will include multiple berths with quay walls that can extend over 2 kilometers in length. For sake of simplicity, in this exercise let’s assume we are building a 2 million TEUs container terminal with a quay wall length of 1,000 meters and 10 STS cranes (assuming 200,000 TEUs per crane). Behind the quay wall we are designing a fully automated container yard with 24 automated stacking cranes (ASC). At the outset, an initial estimation expects an investment of no less than USD 400 to 500 million.
CRANE COST
STS cranes require an average investment of USD 10 million per crane, while ASC cranes cost a minimum of USD 4 million each. The total investment cost for 10 STS cranes (USD 100 million) and 24 ASCs (USD 96 million) will therefore total around USD 196 million.
CIVIL WORKS
The ratio between civil works and equipment can vary depending on the size of the projects and the underlying designs. For bigger projects, the civil component is typically lower than for smaller ports, however civil works remain the largest part of any green field investment. We can estimate the costs for building a new quay wall at USD 120 million, of which piling will consume a large chunk (estimated at USD 30 million). When designing the foundation for an ASC track, there are a variety of options each with a different cost implication. Crane rails can be founded on tie and ballast, concrete slab or a piled crane beam. In addition, when deciding on the design of the foundation, it is important to make a trade-off between initial investment cost and future maintenance cost, on top of the obvious analysis of soil investigations. Assuming a piled foundation with 12 aisles of 350 meter length, we will need to build 8,400 meter of crane beam which will set us back an estimated USD 150 million (including yard, buildings, engineering, utilities). This brings the total cost for civil works to an estimated USD 270 million, or more than 30% above the crane cost. Adding 10% for project management, engineering consultancy and other auxiliary costs brings us to nearly USD 300 million worth of civil contracts.
RAIL SYSTEM
Now where does the crane rail system fit in? Between the concrete civil works and the cranes, the crane rail system is a mission critical item that could literally paralyse the operations of an entire terminal if not considered carefully.And what about the cost? In the above example, and depending on location, steel prices and underlying design, a quality rail system for ‘our’ gateway terminal will likely require an investment of anywhere between USD 3 and 5 million, or approximately 0.8% of the entire project value.
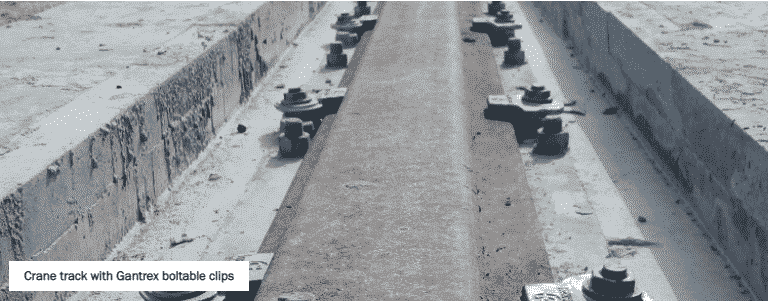
SELECTION OF A CRANE RAIL SYSTEM
wheel loads as high as 180 metric tonnes per wheel – this is roughly the weight of 60 full-size cars on a square surface the size of an iPad mini – it is important to work with an experienced crane rail partner to design the system and supply top quality components. A quality crane rail design will include what is commonly known as a soft mounted solution: a combination of rubber-nosed rail clips to hold the rail laterally but allow a certain amount of vertical and longitudinal movement (due to thermal expansion) with a steel reinforced rubber pad underneath the rail to dissipate crane loads and eliminate unevenness between rail and the supporting structure. This system was developed in the 1960’s and has been perfected by Gantrex 5 years ago with the development of the patented RailLok series of clips and pad specifically designed to fit properly against the rail and eliminate the ingress of dirt and sand underneath that could potentially destroy the pad component over time. Of course, there is more to a crane rail design than merely the selection of the correct rail clips and pad. One must think about the selection of the correct grout, anchoring system, welding procedures, corrosion protection, rail earthing, possible adjustment. For future settlement, etc.
As important as design and material quality, is the installation of the rail track. There are a number of key activities in the installation process which require a top-notch installation company, among which rail welding, plate grouting, and rail alignment require special skills. Depending on the lifetime travel length of the cranes (larger or smaller than 50,000 km) the installation tolerances selected are ISO12488-1 (or equivalent), Class 1 or Class 2 (as Class 3 is not commonly used for cranes in container terminals.) The real challenge when installing any rail system, which separates the experts from the rest, is to install the rails within the required tolerances (a work of millimeters) whilst keeping as much as possible of the available clip adjustment for future realignments. Indeed, more often than not rails require realignment after a few years when the foundation has fully settled. Often the rail installation is forgotten to be as important as the design and supply, resulting in theoretically top-notch systems performing below expectation, sometimes with disastrous and expensive consequences. When selecting a crane rail partner, engineers should always keep in mind that a relatively small saving at design stage could potentially result in thousands of dollars in operational loss once the project is finished: USD 35,000 per day, or in the above example USD 350,000 per day for all (10) quay cranes.
DISCLAIMER
The above cost estimates are the result of field research and discussions with industry specialists. They should be considered best estimates intended to provide the reader with a ballpark picture of the investment and operational costs of container terminals around the world, and are for all intents and purposes non-binding to anyone who has contributed to the research. Gantrex is the global market leader in production, distribution, installation and maintenance of high quality crane rail solutions. Gantrex’ products are used in many different applications and end-markets including ports, shipyards, steel mills, aluminium smelters, railway depots and heavy industries.